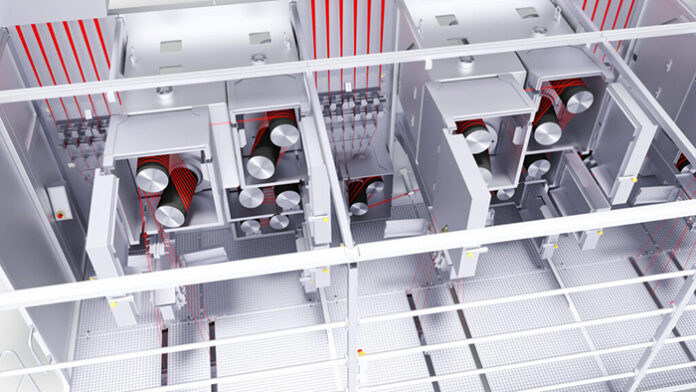
As a traditional textile country, India has also established a strong position in the field of manmade fiber production in recent decades. The West Asian country has now become the second largest polyester yarn manufacturer in the world. The Indian textile industry covers the entire value chain from the melt to the finished textile end product.
The technical textiles sector in particular is regarded as a future market. With an average growth rate of 12% since 2013, this dynamic sector accounts for around 13% of the entire Indian textile and clothing market, according to the government organization Invest India. The market volume has almost doubled in the past ten years. In India, the production of industrial yarn has so far relied heavily on polyamide. Oerlikon Barmag has a strong market position here. “In recent years, we have commissioned plants for numerous customers,” says Dr. Wolfgang Ernst, Head of Sales of the Oerlikon Business Unit Manmade Fibers Solutions.
Increasing demand for industrial polyester yarns
The construction boom and the increasing use of geotextiles and industrial textiles in various infrastructure projects as well as in agriculture and aquaculture show enormous growth potential. This is supported by the government’s 2021 industrial development program, which includes technical textiles as one of ten priority sectors. The program is based on reducing dependence on imports. Until now, a large proportion of the technical textiles and yarns required in the country have been imported.
Increasing demand for industrial polyester yarns The construction boom and the increasing use of geotextiles and industrial textiles in various infrastructure projects as well as in agriculture and aquaculture show enormous growth potential. This is supported by the government’s 2021 industrial development program, which includes technical textiles as one of ten priority sectors. The program is based on reducing dependence on imports. Until now, a large proportion of the technical textiles and yarns required in the country have been imported.The trend towards high-quality technical textiles for the domestic market has also been noted by the Remscheid-based machine and plant manufacturer. “We are receiving more and more inquiries from Indian customers for spinning systems for industrial yarns,” says Dr. Wolfgang Ernst. “What is new is the great interest shown by companies from downstream processes that are looking for backward integration. We attribute this to the stricter regulations of the Bureau of Indian Standards. Until now, industrial yarns were mainly imported from China. In order to guarantee the quality of the processed yarns, this has been strictly regulated by the government since last year. It therefore makes sense for Indian textile producers to enter the yarn manufacturing sector.” This development was also noticeable at this year’s Techtextil in Frankfurt, where the experts from Oerlikon Barmag were able to hold a disproportionately high number of technical discussions with Indian customers and interested parties.
Oerlikon Barmag’s industrial yarn technology offers an extensive process window – without compromising on yarn quality. The flexible spinning concepts enable a variety of possible yarn products for numerous applications. The portfolio includes processes for the production of polyamide and polyester yarns with the required physical properties for a wide range of end applications. Whether HMLS yarns for car tires, yarns for geotextiles, safety belts or even airbags – yarn producers will find a tailor-made concept for every end application at the Remscheid-based solution provider.