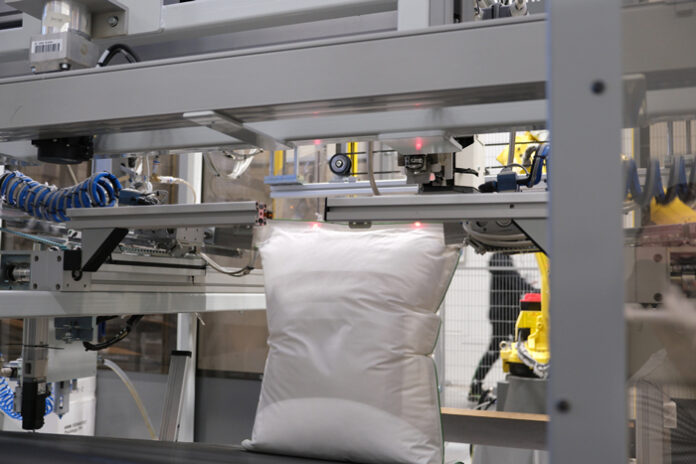
Continuous investment in the latest automation technologies – involving a long-standing and close cooperation with TMAS member ACG Kinna – has ensured family-owned Värnamo Sängkläder AB has retained its leading position in the production of high-quality bedding against heavy odds.
At the recent Heimtextil exhibition held in Frankfurt, Germany, from January 9-12, Martin Åhlander – the third generation CEO of Värnamo, which has specialised in high quality Nordic bedding since its foundation in 1951 – explained that his company is now the only producer of pillows, mattress protectors and quilts with manufacturing remaining in Sweden.
Investment
“Around fifteen years ago, our competition from Asia got very intense, as companies over there started exporting bedding products of very high quality at much lower prices than we could possibly produce conventionally in such a high-cost country as Sweden,” he said. “Our solution was investment in the latest automated technologies, enabling us to be both flexible and to respond very quickly to the needs of our customers while cutting costs. This has proved to be a winning approach.”
Värnamo first started collaborating with ACG Kinna in the 1980s, initially with the installation of automated overlock stitching units for quilt production, followed by further moves such as bringing in-house polyester ball fibre filling technology into its plant with Nowo filling machines.
High volumes
In a more recent development, Värnamo became one of the very first companies to install an ACG Kinna robotic pillow line.
With the ability to fill and finish some 3,840 pillows in an eight-hour shift, this line configuration enables the completely seamless fibre handling, filling, sewing and packing of pillows.
“We needed big volumes to enable such an installation, and they were forthcoming,” Åhlander said. “We are now producing and supplying eight times more pillows than we did before the installation, so we’re pretty happy about this decision.”
“Since the Covid-19 pandemic there have also been increasing problems with the logistics and cost of international shipping, leading to very long lead times for products from Asia on occasions, which has worked in our favour too,” added Martin’s mother and Värnamo’s sales manager Berit Åhlander Nilsson.
Complete process
Nowo – a long-established name in fibre filling technologies – became part of ACG Kinna at the end of 2021 and most recently, EyeTech, a young, Swedish developer of machine vision solutions for manufacturing, warehouse and factory automation has also joined the company.
“EyeTech exploits 2D, 3D and deep learning techniques for inspection, measuring, and robot guidance and is further enabling us to fulfil our promise of ‘complete process – one supplier,” explained ACG Kinna marketing and sales manager Tomas Aspenskog. “We now provide complete customised automation for the entire production chain – from the opening and weighing of the fibre to the packaging of the final products.
“With one partner, one installation and one freight delivery, each customer’s needs are individually covered, eliminating the headaches that arise from trying to coordinate multiple suppliers during a new installation. Värnamo is the flagship showroom for our automation capabilities and because they are so close to us, we often take other potential customers on visits to them, in order to fully demonstrate what is possible.”
“Our relationship with ACG Kinna is beneficial to both companies and we’re constantly exchanging ideas on both new process and technology improvements,” concluded Martin Åhlander.

Heimtextil 2024
“ACG Kinna had a very successful Heimtextil 2024, along with another TMAS member, Automatex, which is developing further technologies for home textiles with the emphasis on fully automated and highly integrated production lines,” said TMAS Secretary General Therese Premler-Andersson. “These technologies enable significant resource savings to be achieved, while making production in high-cost countries once more profitable. Cost effective manufacturing closer to the customer is also more sustainable, while enabling companies like Värnamo to change their cost structures but also increase their capacities and flexibility.”