LMW and Sri Lakshmi Ganesh Spinning Mills’ longstanding partnership for OE Recycled fibre processing has been instrumental in setting benchmarks for producing recycled yarn. LMW’s smart series machinery has enabled Sri Lakshmi Ganesh Spinning Mills to process recycled fiber efficiently while ensuring the highest productivity & quality.
The inspiring journey of Sudhan Group traces its origin back to a humble yarn trading venture in 1985, the ethos of quality and growth has remained unchanged. Today, under the dynamic leadership of Mr. K C Chandrasekaran, Managing Director, and Mr. A C Hariharan Sudhan, Joint Managing Director, Sudhan Group has blossomed into a multifaceted enterprise, encompassing every stage of textile production. With over 1200 dedicated employees, Sudhan Group has evolved into a powerhouse, catering from fiber to fabric to trade, with an unwavering commitment to quality and customer satisfaction.
“Our partnership with LMW has been instrumental in transforming our spinning mill. With their latest technology and innovative solutions, we’ve boosted efficiency and cut operational costs. Most importantly, their support has led to a quicker return on investment, fueling our growth and setting new standards in our industry.” Mr. K C Chandrasekaran, Managing Director Commencing with a modest setup of 960 rotors for cotton processing, Sri Lakshmi Ganesh Spinning OE division mill quickly recognized the need for sustainable practices in the industry. With a forward-thinking approach, they transitioned into recycled fiber processing, aligning with global demands for eco-friendly solutions. Today, their capacity has surged to a remarkable 10,000 rotors, with M/s. Sri Lakshmi Ganesh Spinning Mills contributing 5,000 rotors and M/s. Sudhan Yarns adding another 5,000 rotors to the group’s portfolio.
entral to their sustainable journey is the integration of LMW’s Smart machines, meticulously designed for efficiency and environmental consciousness. LMW’s cutting-edge technology, including the revolutionary Autoblend LA10 system, has been instrumental in optimizing resource utilization while ensuring uncompromised quality. With a production capacity of 40 tons per day and a range spanning from 2s to 36s Ne recycled yarn, the mill caters primarily to domestic markets, championing the cause of sustainable fashion at a grassroots level.
LMW’s State-of-the-art machinery at Sri Lakshmi Ganesh Spinning Mills
LMW has recently supplied its state-of-the-art preparatory machinery for processing regenerated fibre at the mills. The installation includes Blowroom Line comprising of AUTO BLEND LA10, MIXING OPENER MODEL LB3/7, UNIMIX MODEL LB7/4 & LB7/6, Card LC361 – 5 nos. and Autoleveler Draw frame LDF3 S – 2 nos.
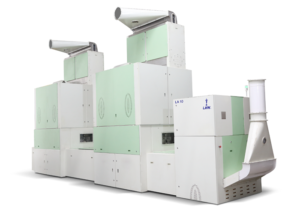
The Gentle Blowroom line from LMW ensures efficient opening, cleaning, and homogeneous blending. This highly flexible blowroom line, can process Regenerated fibres, Cotton, Manmade Fibres, Blends, and Special fibres with high cleaning efficiency. The Blowroom line is equipped with Autoblend LA10 and assures high accurate blending up to 1% range and has a high production capacity of 2000 kg/hr, effective micro dust extraction and continuous feed to the Card.
The Gentle Blowroom line from LMW ensures efficient opening, cleaning, and homogeneous blending. This highly flexible blowroom line, can process Regenerated fibres, Cotton, Manmade Fibres, Blends, and Special fibres with high cleaning efficiency.
The Blowroom line is equipped with Autoblend LA10 and assures high accurate blending up to 1% range and has a high production capacity of 2000 kg/hr, effective micro dust extraction and continuous feed to the Card.
- Maximum, 4 Feeder
- Blending ratio up to 99:1
- Blend accuracy of +/- 1%
- Two-line output possible with two different blend %
- Direct measurement using load cells
- Min. 100 gms to a maximum 3000 gms per drop
- Max. handling of material in Blending Chamber is 5500 gms/sandwich block (Depends on Tuft Size & Blend%)
- Manpower reduction in mixing department
- Blend Accuracy +/- 1% : Accurate weighing of material
- Lot size can be set for each blend
- Two lines with different blend ratios are possible Online weight variation monitor which monitors weight & stops the machine if there is weight variation
Card LC361 – Equipped with single licker-in and is designed for higher productivity and quality with distinctive features for every variety of cotton, man-made fiber, recycled fiber, and blends. The machine has a special profiled Arcual combing arrangement for lesser lint loss, the Highest number of working flats (36 nos.) and the Highest Active Real Carding Area of 1.296 mtrs result in 20% higher carding area. The robust manufacturing and design of the card ensures the reliability of the parts during the processing of recycled fibers.
Autoleveller Draw Frame LDF3 S – Equipped with a servo drive arrangement and a well-synchronized drive system with a timing belt. It is specifically designed to operate at a maximum delivery speed of 1,100 mpm (mechanically), enabling high productivity while maintaining consistent sliver quality for counts up to Ne 36s in recycled hosiery and woven applications. The advanced Duo Digital Autolevelling system optimizes the process, resulting in consistently improved sliver quality at higher speeds.
“The exceptional performance of LMW’s products, particularly the Autoblend system, meets and exceeds our expectations in productivity, quality, and related deliverables. The Autoblend’s perfect blending capabilities have streamlined our processes and saved manpower. LMW’s solutions have been invaluable.” says M J Senthil kumar, General Manager
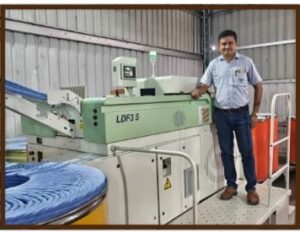
LMW’s Sustainable Smart Solutions for Spinning Success (4S), supported by a culture of innovation, empowers mills with a technological and competitive advantage. This is achieved through mission-critical automation, real-time data, analytics from connected machines, compatibility with all applications, and reliable performance under diverse operating conditions.
At LMW, Sustainability & Circularity is a way of life,
LMW consistently strives to minimize the impact of its manufacturing processes on the environment. As sustainability has become an integral part of its DNA, LMW has pledged its time and resources towards this worthy cause. Sustainability also means extending the lifecycle of the products and LMW has been producing machines that are built to last.
LMW RESPIN
Transforming the textile value chain into one that is sustainable, and circular will allow manufacturers to address the environmental and social impacts, while also supporting people, prosperity and equity. The Smart Series machines from LMW, the Trendsetter in recycled fibre processing is suitable for mechanical recycling and is the most popular one with over 100 installations globally.